One of the shortest descriptions which can be made about industrial coatings is that they are a chemical, organic or inorganic, film/layer applied on media/substrate, defined by their protective rather than their aesthetic properties (although they can provide both), and depend on the visibility of the particular application.
Industrial coatings can be catalogued into several main types, however in this article we will focus on the so-called, high performance protective coatings, which have a broad application in both refining and petrochemical processing plants.
The most common use of protective coatings, is for corrosion control. In the downstream and energy industry, it has been proven that the best materials for such films, are the inorganic silica and metal oxides based ceramic materials.
When looking at reducing overall OPEX and CAPEX costs, reduction implementing protective coating technology in key refinery units, gives a significant advantage for the operator. Many operators are focused on minimizing financial losses due to unplanned shutdowns and maintenance operations, all caused by an unpredicted corrosion erosion process.
Refinery equipment such as fired heaters, furnaces, heat exchangers, condensers, and tubular reactors are not only operating in severe conditions (such as temperature and pressure amplitudes) but also processing a varieties of crude blends containing corrosion active impurities such as chlorides, organic acids, elemental sulphur and sulphides, and a specific type of bacteria which cause microbiologically influenced corrosion (MIC). Ceramic coatings can help operators minimise their corrosion erosion and fouling risks caused by the above factors.
"A picture is worth a thousand words"
Adage in multiple languages
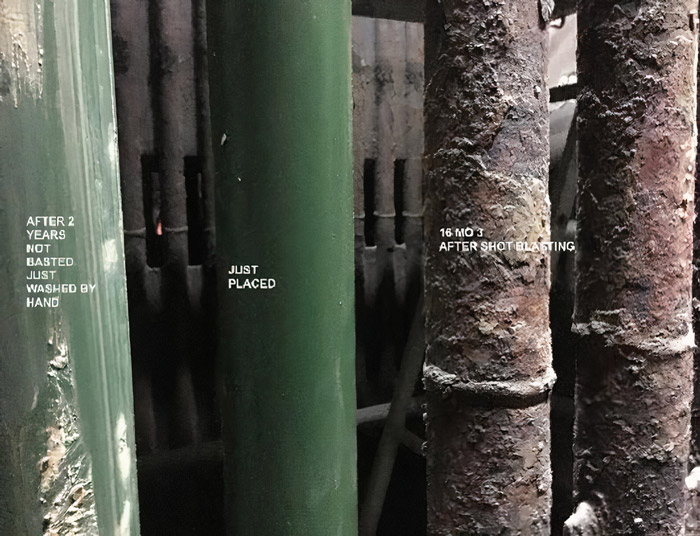
Picture 1. Steam reheater pipes outer side coated, from left to right:
1st pipe - coated pipe after 2 years of service (washed by hand)
2nd pipe - a brand new coated pipe
3rd and 4th pipes - 16Mo3 type blasted after 2 years of service
Source: TUBACEX Group, S.Lodha.
Depending on the refinery application, inner and/or outer coated tubes help reduce overall processing facility opex costs, due to the following improvements:
- Cleaning frequency reduction
- Increased transfer efficiency
- Improved fuel/energy consumption and efficiency
- More effective spalling, whether online or pigging methods
- Increased Operational Span
As a result, the performance coatings result in a reduced carbon footprint.
Operators, especially the ones processing heavy crudes in a higher NCI configuration (>10), face inner pipes fouling issues, when going further downstream and closer to the bottom of the barrel (VDU fired heaters, visbreakers and delayed coking units).
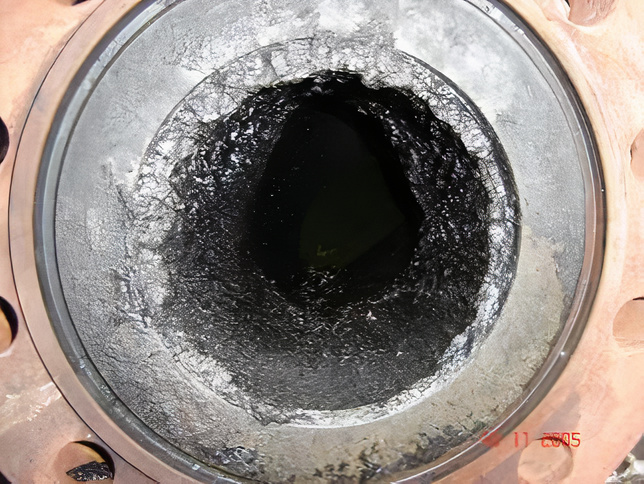
Picture 2. Non-coated bottom of the barrel pipe – internal coke deposits accumulated
Source: TUBACEX Group, S.Lodha
If not precisely tuned, Residue Upgrading units can accumulate coke formation within the inner process pipes. As the coke layer grows, the effective heat and flow transfer is reduced, causing running conditions requiring a unit shutdown, mechanical pigging or online spalling maintenance on reduced intervals.
Performance coatings won’t solve the cause of such issues, however their key properties are outstanding anti-fouling resistance – the coated surfaces are as smooth as glass due to the silica properties, capable in reducing approx 97% of the roughness of the base material. So, instead of fouling within the pipe, the potential coke formations will have another end-up point, which will be the preferred option for each refinery maintenance team – clogged filters are the lesser “evil” compared to clogged pipes.
Performance coatings do not require additional space in a process unit, usually the thickness of the ceramic layers is less than 200 microns (0,2mm), but still able to provide excellent corrosion and abrasion resistance, since the coat is chemically bonded to the substrate media, while being chemically inert and resistant up to 800 °C.
On the rheology side, clogging hardness properties are harder than any steel pipe, meaning it can combat the harsh impact of Sulfuric Acid, Hydrochloric Acid, Soda Ash and other active compounds and impurities.
The solution can be considered a big plus for operators – reduced capex and opex costs, lower fuel and energy consumption, therefore increased energy efficiency and less emissions, whilst ensuring smooth operations and last but not least increased safety and reliability, since the unplanned shutdowns and maintenance are significantly reduced.

Published by:
